In modern manufacturing, automation equipment has become a key factor in improving production efficiency and product quality. This case of a fully automatic online coiler in our project of South America is an example to prove.
Information of Project:
Region: South America
Coiling products: HDPE solid wall pipe
Coiling pipe diameter: Ø16 — Ø32mm
Production line speed: 30m/min
The original semi-automatic coiling machine required manual roll change and packaging, and the coiling speed could not meet the production speed of the extrusion line, which forced to reduce production efficiency. Customers have non-standard requirements and have special requirements for the wall thickness of pipe products:
· Very thick wall thickness: The wall thickness of the 32mm pipe exceeds 5mm, and the tension control of the automatic coiling and the bundling treatment of the pipe end are very high.
· Very thin wall thickness: The wall thickness of the 16mm pipe is only 2mm. Under the limited inner diameter of the coiler, it is necessary to ensure that the pipe does not deform during winding, and there are special requirements for coiling design and program control.
Solution: We has customized a fully automatic coiler for “extra thick” and “extra thin” pipes for customers, equipped with automatic PP strapping and automatic unloading functions. The equipment adopts a full servo system and laser ranging closed-loop tension control, and the servo strapping head “arrow-through” PP strapping method ensures that the pipes are neatly arranged and beautiful within the minimum coiling radius, and the winding speed reaches more than 50m/min, which greatly improves the customer’s production capacity and reduces labor costs.
Automatic Pipe Coiler improve Efficiency and Precision
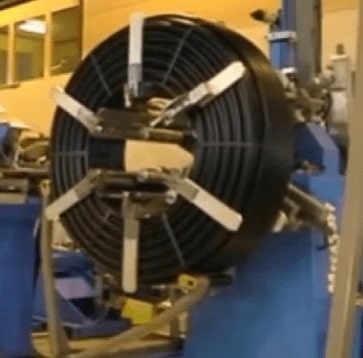
Our pipe coiler adopts a double-station design, which can provide customers with two sets of coiling devices working alternately, reducing the downtime of core replacement and improving production efficiency. The winding adopts closed-loop tension control to adapt to the different production speeds of customers, and is equipped with automatic pipe clamping, pipe cutting and roll changing devices to reduce customer manual operations, improve production safety and efficiency, and reduce labor costs.
Bundling and Packaging: Ensure Perfect Protection of Products
The equipment adopts an advanced servo motion control system to bundle the pipes, and automatically feed and tighten the belt to ensure the firmness and beauty of the bundle. In addition, the strapping mechanism adopts PLC electrical control, has an anti-slip function, and is equipped with a strap storage component to achieve intelligent and efficient strapping operations, improve overall strapping efficiency, and facilitate pipe storage and transportation.
Automatic Unloading: Ensure the Safe Discharge of Strapped Pipes
After the PP strapping is completed, the manipulator automatically unloads the strapped pipes to the ground. In addition, the equipment is equipped with a heavy-duty unloading arm that can bear a maximum load of 60kg and adopts a flexible unloading method to prevent the pipe from falling and damaging the surface.